Enlighten Continuous Improvement Practitioner program
This Lean Six Sigma Yellow Belt accredited course is designed to equip your team with the skills and tools needed to drive improvement, increase efficiency, and deliver substantial ROI. Participants will learn to use Enlighten’s CI Framework and data to identify and solve business problems, manage projects effectively, and navigate change. Empower your supervisors, team leaders, and managers to excel in their roles, engage your workforce, and foster a culture of continuous improvement. Join us to unlock new dimensions of problem-solving and sustainable growth for your business.
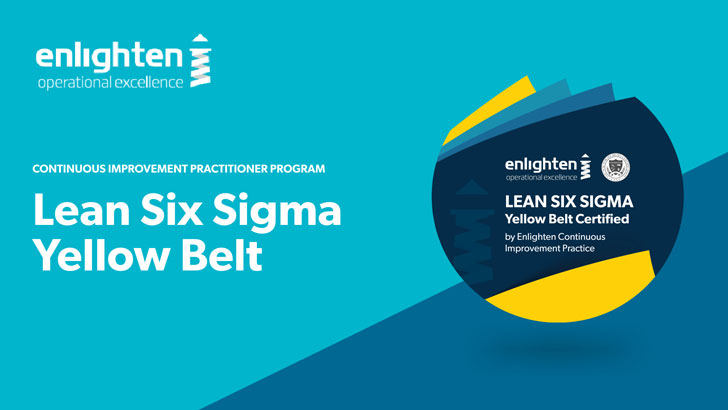
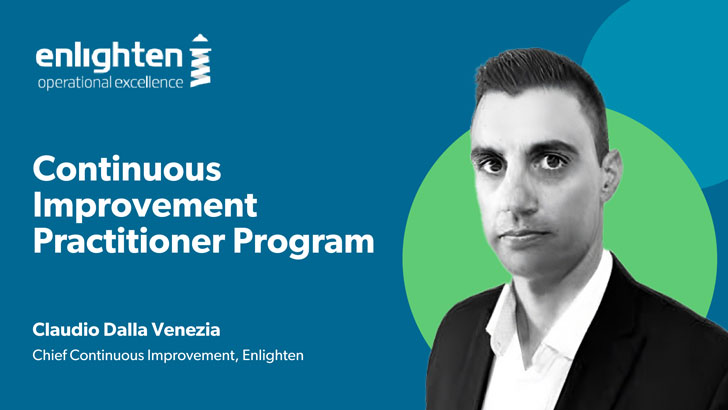
Enlighten Continuous Improvement Framework Drives Results
Utilising Lean methods and the scientific approach to transform business processes and remove substantial amounts of waste, the Enlighten Continuous Improvement Framework is a highly collaborative model tailored to achieve measurable results along with outstanding customer satisfaction.
GREATER CAPABILITY WITH
ENLIGHTEN SOFTWARE 3.3.0
The Continuous Improvement Practice
Use Lean methods and the scientific approach to transform business processes and remove waste.
End-to-End Optimization
Transformational change | System-wide | Process width | Solve systemic problems
Continuous Improvement
Team level | Individual process/es | Process depth | Removal of waste
Continuous Improvement Training
Lean practitioner | Lean Six Sigma Green Belt | Lean leader | Waste removal
Projects
Proven project delivery framework to help clients meet business objectives
Fulfil / Augment
Fulfil or supplement clients’ continuous improvement capabilities | Projects | PMO | Training
DO YOU WANT TO TRANSFORM YOUR OPERATIONS?
6 Reasons Our Approach Delivers
Change Management
Business Engagement
With the help of a strong engagement model with the business, we ensure business objectives and priorities are met.
Governance & Buy-in
Our approach involves structured project governance and senior management buy-in to drive accountability for results.
Enlighten Data
Our team members are experts at using Enlighten data to facilitate successful, swift and sustainable change.
Proven CI Framework
Our proven CI Framework solves problems and delivers value. We do not just provide recommendations and walk away.
Skills & Expertize
Our team has significant experience leading different types of transformation projects to deliver sustainable improvement.
Case Studies
Reduce Clarification / Research Waste within Claims Adjustment Business Area
Reduce Inventory Ageing within Back Office Processing Area
Moving Client Services from a Reactive Organization to a Proactive Organisation
Quality Management Framework to Reduce Manual Checks based on Data-driven Decisions
Reduce Clarification / Research Waste within Claims Adjustment Business Area
Project Context:
The Enlighten Continuous Improvement Practice identified a significant Opportunity to reduce Clarification and Research Waste within a Claims Adjustment Business Area, comprised of ~ 110 FTE. Waste identified equated to 18% of the total resources in the business area. Project timelines were 15 weeks and I.T. changes were out of scope for the project.
Project Goals
Reduce waste (‘Clarification and Research’ category) by 15 – 20% within a 15-week timeframe.
Upskill the Claims Adjustment Supervisors and Managers on Lean tools and methods to shift the organization to a Continuous Improvement mindset.
Key Pain Points
SOP’s and decision-trees to make adjustments are not well documented and open for interpretation. Furthermore, best-practice for complex scenarios are not documented and shared.
People allocated to work / scenarios they are not familiar with and lack exposure and experience.
Operations not providing notes/information as to why adjustment is started which increases time Clarification and Research time.
Key Solutions
Redesign SOP’s, training material and decision trees for Operators to effectively make adjustment determinations.
Development of a Learning Ecosystem (using MS Teams) to dynamically share Best Practice and update SOP’s / training material.
“Assist Line” capability for Operator Support on complex determinations / scenarios.
Improved allocation of work based on Operators skills / experience / exposure using Enlighten Planning module.
Project Results
Project delivered a 2:1 Return On Investment (ROI), as result of removing 42% of ‘Clarification and Research’ waste.
Systematic and automated control mechanisms empowered Supervisors to effectively sustain gains delivered by the project.
Skills transfer of Lean principles, methods and tools allowed Line Managers to identify further improvement opportunities.
Reduce Inventory Ageing within Back Office Processing Area
Project Context:
A Back Office Processing Area’s inability to meet Market requirements for processing cycle times was negatively impacting a Health Insurance provider’s ability to increase sales. Enlighten’s Continuous Improvement Practice was hired to improve processes and reduce Inventory Ageing. The Back Office Processing Area is comprised of ~75 FTE’s.
Project Goals
Reduce 4+ days aged Inventory Items from 36% to 15%.
Achieve reduction without the need for client IT changes / solutions (focus on levers and changes within sphere of control).
Identify automation and technology opportunities to prioritize and maximize investment.
Key Pain Points
Process inefficiencies which included failure demand, errors, poor process design and non-value added activities.
“Duplicate Requests” received from clients due to multiple channels available and no status updates on Inventory items.
Misrouted inventory from other Business Areas.
Key Solutions
Redesigned Future State processes reducing waste, bottlenecks, WIP to improve overall flow via a Pull system.
Driving clients to online service channels which provides expectation on processing times and status updates on Inventory.
Engagement plan with Business Partners to track and address misrouted inventory.
Project Results
Reduce 4+ days aged Inventory Items from 36% to 2%.
Identified ~$1 Million benefits for technology and automation investment.
Moving Client Services from a Reactive Organization to a Proactive Organisation
Project Context:
Client Service Organization within the Asset Management domain, comprised of ~285 FTE, desired to increase the time spent on proactive activities to drive key business outcomes such as Increased Sales, Improved Customer Satisfaction, Profitability, Continuous Improvement, Enhanced Product Offerings, etc.
Project Goals
Establish a framework, using the Enlighten Software, to measure the time spent on proactive, operational and reactivities activities along with Obstacles impeding Client Service teams.
Employ to Continuous Improvement methods / tools to increase the time spent on Proactive activities from 2% to 20%.
Key Pain Points
High number of queries received from internal Operational areas due to Client Services knowledge of internal processes and products.
Ad hoc and unstandardized way in which work is received from internal areas without clear SLA’s – significant email maintenance.
Client Service teams performing Operational activities.
Key Solutions
Development of Knowledge Management repository, processes and SOP’s to empower Operational areas to self-serve.
Configuration of Inquiry Management software to standardize the way work is received, establish SLA’s & reduce email maintenance.
Rationalization of Client Service activities to transition work back to the “correct” Functional/Operational areas (free up CS time).
Project Results
~82 FTE’s worth of capacity (~$4.9 M) freed up to focus on Proactive activities.
Capability to continually monitor time spent on proactive activities.
Improved lines of communication and engagement between Client Services & Business partners based on data-driven conversations.
Quality Management Framework to Reduce Manual Checks based on Data-driven Decisions
Project Context:
A Retirement Services Operation (~78 FTE) was on a transformational journey to build a scalable and cost-effective operation. As part of the transformation program, the Enlighten CI Practice was hired to lead a CI project to improve quality (reduce errors), so a risk-based decision could be made to raise the threshold limit on a check-the-checker process to reduce the number of manual checks and create capacity.
Project Goals
Establish an accurate error rate (%) baseline, so that leadership can confidently apply a data-driven, risk management approach to raising the current threshold of $25K to the target threshold of $100K.
Create ~2 x FTE worth of capacity without technology or I.T. enhancements within a 12-week timeframe.
Key Pain Points
Inconsistency in recording Errors and not all Errors being recorded impacts leadership making risk-based decisions.
No Visual Management in place to manage Quality (Errors) – no review and actioning of errors.
Training tools provided are outdated and not user friendly to minimize the potential opportunity for errors.
Key Solutions
Quality Management Framework implemented using the Enlighten Error Waste module to effectively manage Quality (Errors).
Implementation of Visual Management capability (Automated Dashboards) to manage and action Error data from Error Waste module.
Training Development Strategy including update of training tools, best practice sharing, tips & tricks, post training development and buddy system.
Project Results
Accurate and reliable error rate baseline established.
Threshold successfully raised from $25K to $100K which created ~2 x FTE worth of capacity.
Shifted the culture to proactively focus on Quality and adopt a Continuous Improvement mindset.